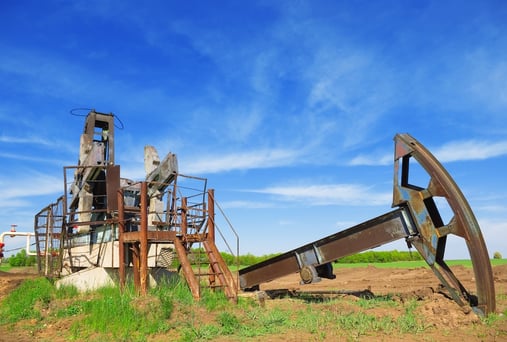
Beam pumps take a lot of abuse. There are tremendous forces exerted on the pump, rod and tubing with every stroke. These forces are dramatically magnified by fluid and gas pound. During restart after pump off, in-rush current wreaks havoc and the force required to get everything moving again can stretch, wear and tear surface and downhole equipment. It is no wonder that beam pumps require multi-day workovers and unscheduled maintenance.
An easy integration of new technology can reduce the severity and frequency of beam pump maintenance. The IronHorse variable speed drive (VSD) integrates into any beam pump configuration including those with pump off controllers (POCs). The IronHorse has an immediate impact on many factors that contribute to early pump failures.
- Power management. The IronHorse reduces peak load demand and uses electricity more efficiently. Because we have no brake chopper/resistors there is no excess electricity wasted or burned off in the form of heat. In-rush current never exceeds the name plate rating of the motor and peak demand is reduced drastically.
- Pump off. The IronHorse VSD with SPOC software controls pump speed, enabling much slower production rates. This allows the pump production rates to match the reservoir inflow rates, eliminating many start-stop cycles which are stressful to the pump and rod string. Additionally, by eliminating much pump “off” time, debris from the production fluid that normally falls out of suspension and into the pump stays in suspension. This can extend the life of the traveling valve. Finally reduced pump speeds decrease the stress on the pump and rod string. By running more slowly instead of running faster and then off, the same number of strokes can be delivered per day at a lower stress level, enabling longer run life.
- Slower Transition Speed. Traditional on-off pump controls with NEMAD motors will accelerate in the low load portion of the stroke. This includes the transitions from up-down and down-up. By operating more slowly at these transitions, we reduce rod compression and harmonics, reducing the stress on the rod string.
- Active Torque Control. The IronHorse VSD can actively limit the torque the motor delivers to the pumping unit. This can be helpful in limiting stress to the gearbox and associated peak loads to the rod string. It is not uncommon to see decreases in peak rod load of 10% with a corresponding increase in minimum rod load.
- Data for trending. The IronHorse collects a large volume of operational data that can be analyzed for trends, including potential maintenance requirements. The analysis can be on location or remotely through SCADA.
- Sensorless Pump Off Control. The IronHorse can be integrated with the POC on-site or use its own built-in SPOC Software. There are no sensors, cord sets or load cells to repair.
Avoiding just one workover saves thousands of dollars and adds as much as 1-2% production. Shifting at least some unscheduled maintenance to scheduled avoids inconvenience, down time, and cost uplifts for quick response.
To learn more about how integrating new technologies like the IronHorse VSD can reduce maintenance and overall lifting costs, see “Drive Down Lifting Costs through Integration.”
